Employee Recognition Ideas for Manufacturing: Boosting Morale and Productivity
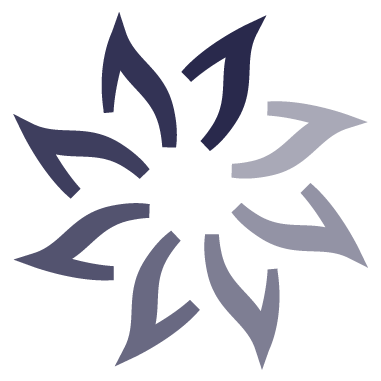
A Global Employee Recognition and Wellness Platform
Manufacturing keeps the world moving. But the people on the factory floor? They often get overlooked.
Their work is demanding, with long hours, repetitive tasks, and, yes, safety risks. It’s not just physically demanding; it’s mentally draining, too. And that can lead to burnout and turnover.
According to UKG’s Manufacturing Industry Report, 62% of manufacturing organizations reported an increase in turnover year-over-year. This statistic speaks volumes about the challenges the sector faces in retaining its most valuable asset — its workforce.
So, how do you keep these crucial workers motivated and loyal? The answer is simple but powerful: employee recognition.
Recognition is not just about a pat on the back; it’s about making employees feel genuinely valued. However, it has to be the right kind of recognition - one that’s timely, meaningful, and fits the manufacturing floor’s reality. Recognition that is delayed or irrelevant simply won’t cut it.
That is why, in this blog, we’ll explore the best employee recognition ideas for manufacturing, explain why recognition matters deeply in this sector, and offer guidance on how to measure its real impact.
Whether you’re a plant manager, HR professional, or business leader, understanding these insights can transform your manufacturing workforce’s engagement and productivity.
Why Employee Recognition Matters in Manufacturing
When employees don’t feel recognized, they start to feel like just another cog in the wheel.
According to PwC, only 48% of manufacturing leaders believe their frontline workers are truly engaged. That’s less than half.
And disengagement isn’t just a culture issue. It affects the bottom line. Disengaged workers are more likely to overlook safety steps, make errors, and lose focus on the task at hand.
Because one thing is clear: manufacturing workers don’t spend their time scrolling through emails on their desks. They are mainly on the shop floor without easy access to digital communication. This makes it challenging to engage and recognize them.
This physical disconnect from traditional office tools creates a barrier. It means many workers miss out on the regular streams of praise, updates, and acknowledgment that desk-based employees might receive daily. Without this, employees can feel invisible, which erodes their motivation.
Recognition changes that. It shows people they matter. That their work is noticed, even if they’re not sitting at a desk.
Whether it’s a shoutout during a shift meeting, a quick “thank you” from a supervisor, or a reward system built for the floor, it all adds up. It tells employees, “We see you. We value you.”
What to Recognize in Manufacturing Employees
When recognizing manufacturing employees, you cannot use vague recognition practices. You need to spotlight what truly matters on the floor.
Here’s where you want to focus:
1. Production Milestones:
When employees meet or exceed their targets or maintain top-notch quality, give them a shout-out. Because, hitting a milestone matters for both the company and employees. It keeps the line moving. For example, recognizing a team that consistently hits 100% of their quotas drives motivation.
2. Safety Compliance:
Safety is non-negotiable in manufacturing. Don’t consider safety rules as just a checkbox on a list. Recognize employees who consistently follow protocols and report hazards promptly.
Reward those who don’t cut corners and contribute to maintaining a workplace free of accidents. Highlighting safety champions sends a powerful message that care and caution are valued equally with speed and output.
3. Teamwork & Leadership:
Manufacturing depends heavily on smooth team coordination. Recognize those who step up to support co-workers during peak times or who take the initiative to train new hires. Leadership is about those who lead by example, solve problems collaboratively, and foster a positive work environment.
4. Innovation & Problem-Solving:
Manufacturing processes are complex and constantly evolving. Employees who suggest improvements that reduce downtime, minimize waste, or improve efficiency deserve recognition. Even small ideas that streamline tasks can have a big impact. Celebrating these contributions encourages a culture of continuous improvement.
5. Attendance & Punctuality:
Reliable attendance is critical to maintaining production schedules. Recognizing consistent punctuality encourages accountability. When everyone shows up on time and is ready, the whole operation runs smoother.
Effective Ways to Recognize Manufacturing Employees
Discussing recognition ideas isn’t enough without the right solution in place to make them effective. In manufacturing, a structured employee recognition program is crucial in ensuring employees feel valued.
According to Vantage Circle’s AIRe report, merely 27% of manufacturing companies perceive the effectiveness of their programs as ‘High.’ It also states that almost all companies in the sector must completely re-evaluate their approach to Recognition Programs.
A comprehensive recognition platform is one of the most powerful tools to improve employee morale and productivity. In manufacturing, such a platform ensures that employees are acknowledged in real-time, making the recognition more meaningful.
These platforms automate the recognition process, allowing managers to quickly celebrate achievements and reward employees. These achievements could be hitting production goals or adhering to safety protocols.
Additionally, these platforms allow personalized rewards, so recognition feels tailored to each worker’s preferences. This creates a culture where employees feel consistently appreciated and are more motivated to keep pushing for higher performance.
Now that we have discussed the importance of a recognition program, let’s have a look at some methods that work well on the shop floor:
1. Peer-to-Peer Recognition
Manufacturing thrives on teamwork. When employees recognize their colleagues, it builds camaraderie and strengthens team dynamics.
Many modern platforms include peer-to-peer recognition program features. It allows workers to send real-time shout-outs to one another. This simple act of recognition boosts morale and fosters a culture of collaboration on the shop floor.
Source: Vantage Recognition
2. Phygital Recognition for Non-Digital Access
One challenge in manufacturing is that many workers don’t have immediate access to digital devices. But that doesn’t mean they should be left out of the recognition loop. You can implement a phygital recognition approach (a combination of both digital and physical recognition) to reach everyone, including those who aren’t constantly connected.
Source: Vantage Recognition
For example, a supervisor or senior leader can handwrite a thank-you note to an employee for a job well done, with a QR code attached. After their shift, the employee can scan the code with any mobile device to access the digital recognition platform and see their appreciation in real-time. This method ensures that recognition is both accessible and meaningful, even for those working away from digital tools.
3. Monthly and Quarterly Awards
Regular recognition is vital to maintaining momentum. Implement monthly or quarterly monetary rewards to celebrate outstanding employees. It can be to celebrate safety leadership, innovation, or teamwork.
Automation platforms can simplify the nomination and voting process. Thus making it easy for everyone to participate and ensuring the process remains transparent.
4. Production-Based Incentives
What’s more motivating than tying recognition to actual goals? Production-based incentives allow employees to earn reward points, bonuses, paid time off, or even flexible work schedules to meet their targets. This aligns recognition and rewards directly with the company's bottom line.
A recognition platform can track milestones and allow employees to redeem earned points for company perks, making the recognition feel more tangible and rewarding.
5. Public & Social Recognition
Recognizing employees on a public stage boosts morale and sets a standard for the whole company. Celebrate top performers on your company intranet, LinkedIn, newsletters, or any other social media platform.
Public recognition boosts individual morale and elevates the company’s culture and brand image. It fosters a competitive yet supportive environment that drives continuous improvement.
Measuring the Impact of Recognition Programs
You can’t improve what you don’t measure. This is especially true in manufacturing, where every decision impacts productivity, safety, and employee morale. Tracking results is crucial to ensure your recognition efforts are working. Data-backed insights ensure you invest in what truly drives employee morale and performance.
Regularly analyze these metrics to fine-tune your program:
1. Engagement Metrics: Find answers to these questions -
- How many employees are getting recognized each month?
- Are more people participating in peer recognition?
Steady or rising numbers here are strong signals that your recognition culture is taking root. When more employees participate, it means recognition is becoming a natural, everyday practice rather than a rare event.
2. Retention Rates: Turnover in manufacturing can be costly and disruptive. Monitor your turnover rates before and after implementing recognition programs. A noticeable decrease in turnover indicates that employees feel valued and are choosing to stay longer.
This saves on hiring and training costs. It also preserves institutional knowledge, which is critical for smooth operations.
Productivity Data: Compare the productivity levels of teams that receive frequent recognition against those that don’t. An uptick in output or quality in recognized teams shows that motivation is translating directly into better performance on the floor.
Recognition acts as fuel, driving employees to sustain and improve their efforts day after day.
Safety Records: Track incidents and compliance rates. Are safety incidents down when employees are regularly recognized for compliance?
If it has gone down, you can be certain that recognition linked to safety has resulted in a reduction in the number of accidents. If it has not, then you must reevaluate your entire recognition program.
Summing Up
Manufacturing employees face unique challenges every day - long hours, demanding tasks, and high safety risks. These challenges make timely and meaningful recognition absolutely essential.
But recognition in these environments can’t rely on the usual methods. These employees aren’t checking emails or scrolling through team chats. So, if appreciation only lives in digital spaces, it misses the people who need it most.
That’s where smart recognition strategies come in. The best programs don’t just celebrate effort—they transform how employees feel about their work. They lift morale, reduce churn, and drive focus where it counts: on the floor, in the moment.
Innovative solutions like Vantage Circle’s Phygital Recognition are rethinking what’s possible. By blending physical and digital touchpoints, they make recognition real-time, inclusive, and accessible, even for employees without a desk.
Because no one should miss out on appreciation just because they’re wearing safety gear instead of a headset.