A Practical Guide To Implementing 5S In The Workplace
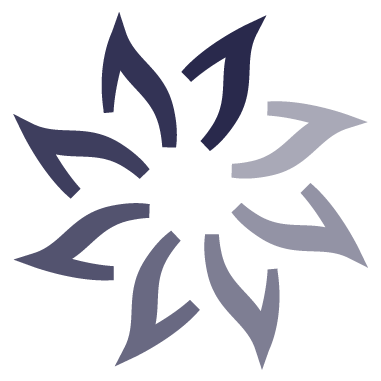
A Global Employee Recognition and Wellness Platform
It's a highly competitive world out there, and everyone wants to grab the top spot. In this rat race, organizations around the world are trying their best to optimize their efforts. Several methodologies are tried and tested to maximize output aided by employee development schemes. And amidst all the methods applied by organizations, one that proved to be uber effective is the 5S in the workplace.
What is the 5S System?
The 5S system is a Japanese set of principles developed by the Toyota Motor Corporation in the late 1960s. This method emphasizes more on workplace organization to increase productivity, efficiency, and safety. All these three factors positively impact employee engagement levels in the workplace.
The 5S System is a lean manufacturing methodology derived from five Japanese terms, namely-
- Seiri, meaning Sort.
- Seiton, meaning Set in Order.
- Seiso, meaning Shine.
- Seiketsu, meaning Standardize.
- Shitsuke, meaning Sustain.
Toyota applied this method in their production framework called the Toyota Production System. And soon, it received the fame of being the leading vehicle manufacturer in the world.
The principles of 5S are not just limited to production processes. Besides, other organizations can apply it to increase safety and reduce wastage in their own set of processes.
Moreover, the 5S program is also one of the foundations of the Six Sigma Principles.
5S - The Five Pillars of a Visual Workplace
The principles of the 5S methodology are termed the five pillars of the visual workplace. Let’s learn about each 5S principle in detail:
Seiri (Sort)
The first principle of 5S goes as Seiri or sorting. It's all about arranging things properly and removing unnecessary items around the workplace. The end goal of this step is to reduce extra clutter to promote better efficiency and avoid mistakes.
How to implement this step?
Start off by asking your employees what is necessary and what isn’t around their workspace.
For example-
-
You can ask your employees if an item is needed?
-
If the item is really required, then try to find its importance?
Once you get the answer, you can ask if this can be moved to a better place for freeing up space?
This should be done really carefully, and only the people using the object should be enquired about it. Make a priority list and assign a secluded space for storing unnecessary items.
After doing it, you'll see how smoothly people can move around, adding to your workplace efficiency. This will further create space for things that your employees actually need to work efficiently.
Seiton (Set in order)
The second step in the 5S process is to set things in order. It is more like visual management, where you need to store things where they're easily accessible and don't cause any issue.
How to implement this step?
Ask your employees the following questions-
-
Which items are used frequently?
-
Who or which team uses them the most?
-
When the item or the equipment is used?
-
How many of those items or equipment could be further required in the future?
Also, ask for their opinion regarding where to place the objects for better accessibility.
After you get the answers to all these questions, you can do the following -
Use tags, shadow boards, labels, and floor markings to denote designated spaces as per their usage.
In case of heavy and risky equipment, use safety signs and notice boards with precautionary measures to alert people working there.
With proper storage management of tools and equipment, you can create a safe working environment.
Seiso (Shine)
The objective of the third principle in the 5S system is to create a clean and well-maintained work environment.
It is a known fact that productive people always keep their workstations clean to save themselves from distractions. Well, the opposite of it is also true, where a clean work environment boosts productivity and level of motivation. It makes the employees feel comfortable and focus on their work.
How to implement this step?
-
Encourage cleanliness with attention to minute details in the initial phase.
-
Make sure the workspaces are cleaned regularly and maintained at all times.
Further, instead of being dependent on housekeeping staff, encourage employees to keep their workspace clean. This will also instill a sense of ownership and also make them responsible for maintaining their efficiency.
Following these steps complemented by the above two principles will help you sustain a healthy work environment.
Seiketsu (Standardize)
The fourth 5S principle is about setting standards for the measures you take across the organization. When you set a definite standard for any process, the effectiveness of it increases many folds.
Standardizing processes help you turn them into habits rather than keeping them as a one-time process.
How to implement this step?
-
Create schedules and divide the tasks noted above among your employees.
-
Keep track of the progress and provide adequate guidance at every step.
-
Take regular employee feedback for optimizing various processes.
For this, initially, you can set reminders or send out emails. In the emails, you can educate your workforce about the effectiveness of the 5S system.
Also, have discussions on how they can take up the same to improve their personal lives.
Shitsuke (Sustain)
We have now reached the last and final principle of the 5S System, i.e., Shitsuke or Sustain.
Implementing the 5S methodology is all about sustaining the positive changes that it brings along. The objective is to optimize the business processes and remove things that obstruct efficiency.
It is not a one-person task, and you bring in all your employees to ensure proper implementation of this principle.
How to implement this step?
-
First, establish proper workplace communication among everyone working there.
-
Second, make them aware of the 5S principles and their importance.
-
Third, present the positive effects achieved so far to motivate and cheer them up.
-
Fourth, make it a part of your company culture and educate new joiners during their onboarding process.
Here, you can also reward and recognize your employees for all their efforts in establishing the 5S methodology. Doing this will encourage them to continue with their 5S practices and keep improving their efforts.
The Benefits of 5S in the Workplace
The 5S system brings along several benefits for businesses of all kinds if applied accordingly. Many organizations implement it as a part of their company culture. With this, they bring employees together to function as a team and prevent obstructions as they proceed.
Here are a few benefits of implementing 5S in the workplace-
Increased Productivity
One of the primary goals of every organization is to increase employee productivity, and the 5S system delivers it effectively. Setting things in order right from the initial stages minimizes the amount of clutter. It lets the employees perform efficiently without getting overwhelmed or distracted. Thus, allowing them to stay focussed and productive.
Maximum Workplace Safety
One of the primary objectives of the 5S system is to uplift the level of workplace safety, combining order and cleanliness. Clean and well-maintained workspaces reduce the chance of mishaps happening during work hours. Further, it gives the employees a sense of security, allowing them to operate with a free mind.
Optimal Waste Reduction
Another reason for implementing the 5S System is to optimize waste management. Adopting the 5S methodology allows organizations to streamline their resource pools and avoid misuse. It is very important for organizations as that’ll help them bring down the cost of operations. At the same time, it is also great for building a positive brand outlook as effective waste management is a buzzing topic in today’s date.
Increased Employee Commitment and Involvement
Once you start off with the 5S methodology, it becomes more like a part of your company culture. With great coordination, 5S principles become a part of the daily work routine for everyone. Employees learn to take up responsibilities and take care of their part of the job to keep their workplace free. This helps in decreasing employee absenteeism and increasing retention within the company.
Implementing and Sustaining 5S Methodology in your Workplace
Though 5S principles are particularly meant for manufacturing companies, others can adapt and mold it as per their needs. This is because the ultimate aim of every organization is the same, i.e., to achieve maximum growth. Hence, implementing the 5S system makes sure that everyone joins in to improve efficiency and productivity.
There's no bar on who can deploy the 5S methodology, so even small businesses can practice it.
Here are a few ways how organizations can implement the 5S methodology and sustain it in the long term-
-
Create teams consisting of at least one manager or a leader who can communicate the end goals.
-
Host 5S training sessions for all employees before you begin implementing any principle.
-
Designate tasks to teams in accordance with their work areas and job function.
-
Hold review meetings with team leaders to track progress and verify results.
-
Run employee surveys to understand the impact of implementing the 5S methodology.
-
Display the positive results and acknowledge the best performers.
Conclusion
The 5S system consisting of seiri, seiton, seiso, seiketsu and shitsuke gives you visual control over your workplace. It allows you to understand the problem areas and solve them before any red tag is raised.
Here eliminating waste is the end goal that comes when processes are really optimized. That is why every workplace should at least give this method a try and see how it positively affects them.